Презентація на тему «Охорона навколишнього середовища під час виробництва і використання металів»
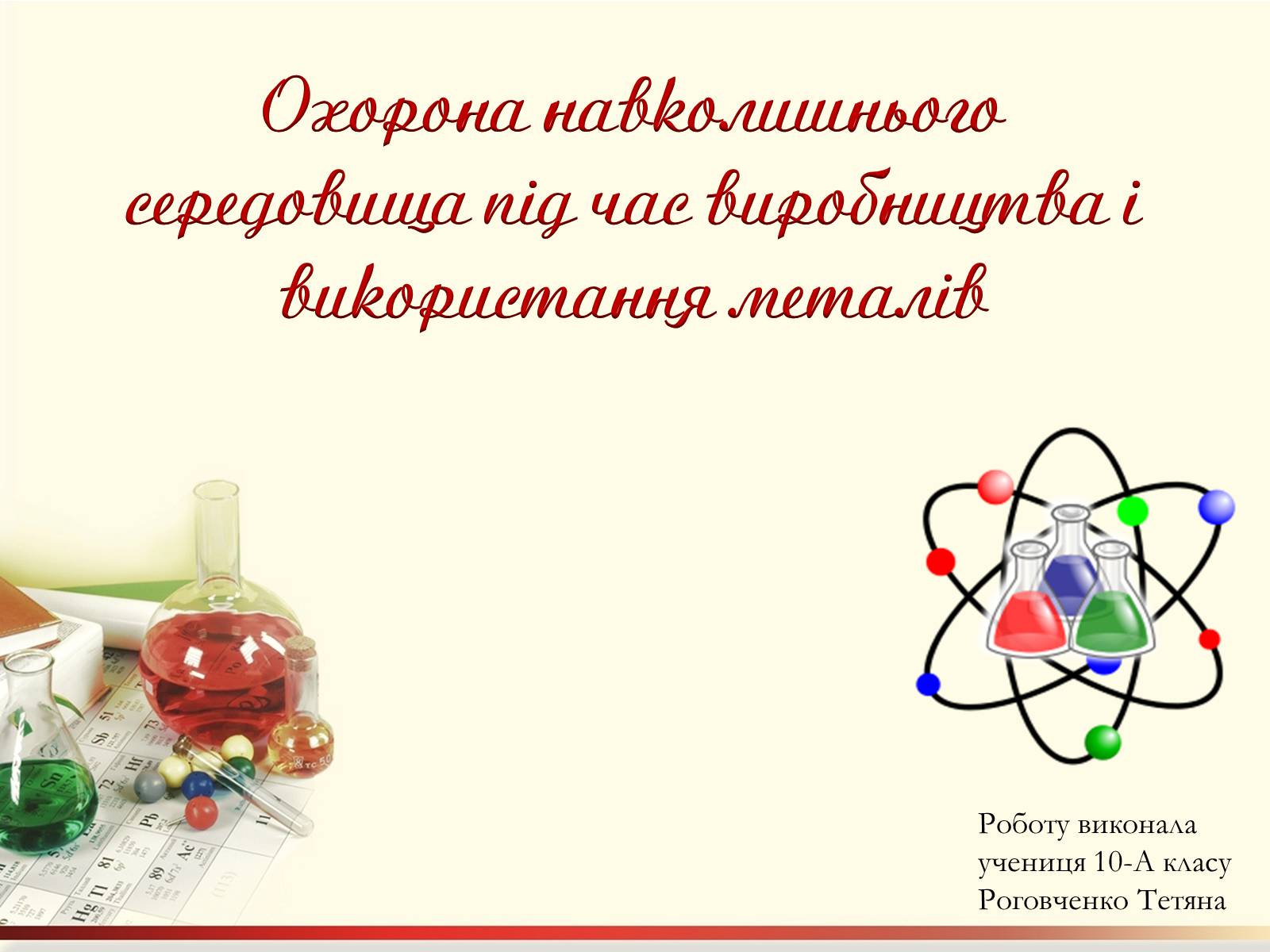
Роботу виконала
учениця 10-А класуРоговченко Тетяна
Охорона навколишнього середовища під час виробництва і використання металів
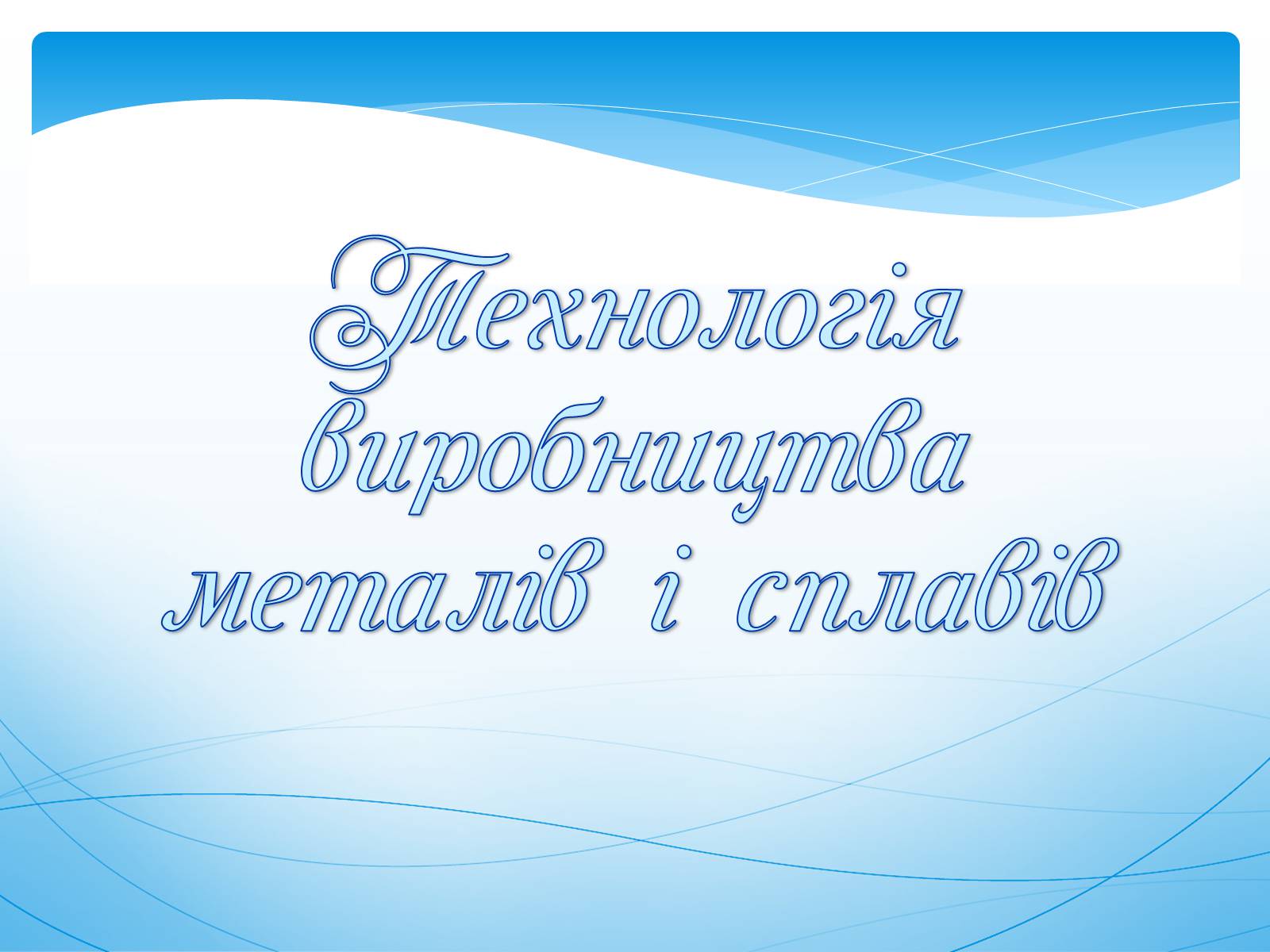
Технологія виробництва металів і сплавів
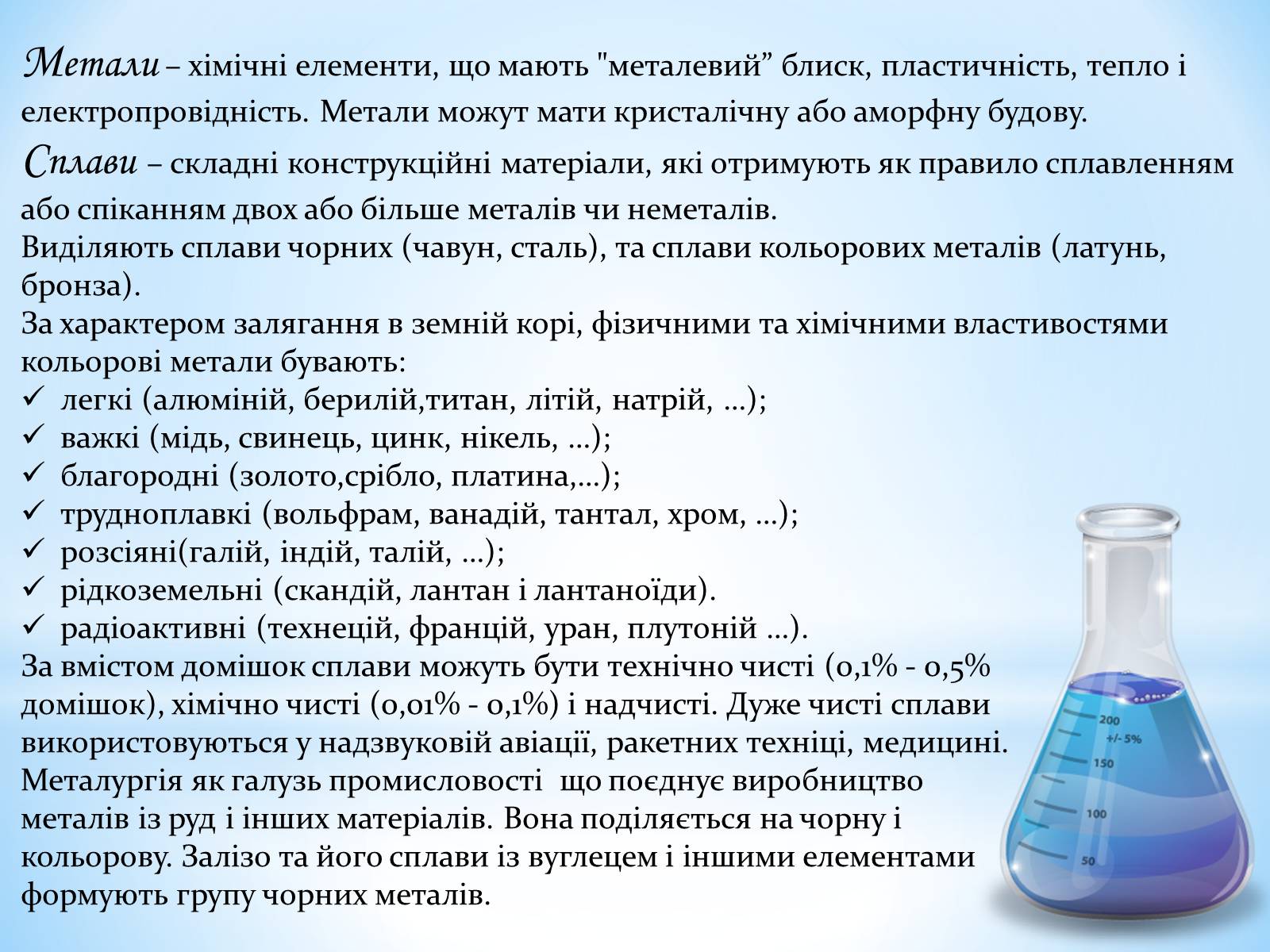
Метали – хімічні елементи, що мають "металевий” блиск, пластичність, тепло і електропровідність. Метали можут мати кристалічну або аморфну будову.
Сплави – складні конструкційні матеріали, які отримують як правило сплавленням або спіканням двох або більше металів чи неметалів.
Виділяють сплави чорних (чавун, сталь), та сплави кольорових металів (латунь, бронза).За характером залягання в земній корі, фізичними та хімічними властивостями кольорові метали бувають:
легкі (алюміній, берилій,титан, літій, натрій, …);
важкі (мідь, свинець, цинк, нікель, …);
благородні (золото,срібло, платина,…);
трудноплавкі (вольфрам, ванадій, тантал, хром, …);
розсіяні(галій, індій, талій, …);
рідкоземельні (скандій, лантан і лантаноїди).
радіоактивні (технецій, францій, уран, плутоній …).
За вмістом домішок сплави можуть бути технічно чисті (0,1% - 0,5%
домішок), хімічно чисті (0,01% - 0,1%) і надчисті. Дуже чисті сплави
використовуються у надзвуковій авіації, ракетних техніці, медицині.Металургія як галузь промисловості що поєднує виробництво
металів із руд і інших матеріалів. Вона поділяється на чорну і
кольорову. Залізо та його сплави із вуглецем і іншими елементами
формують групу чорних металів.
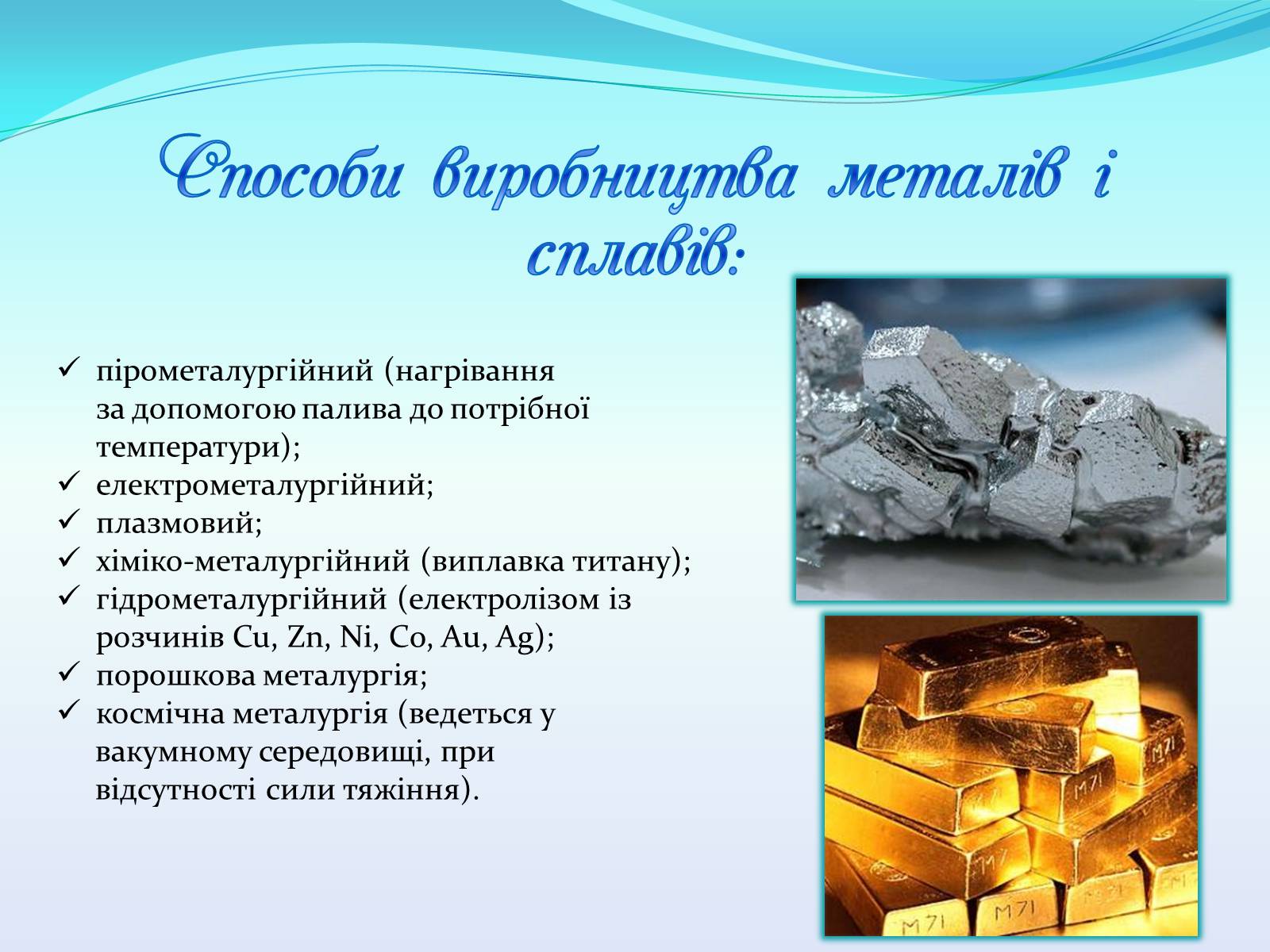
пірометалургійний (нагрівання за допомогою палива до потрібної температури);
електрометалургійний;
плазмовий;
хіміко-металургійний (виплавка титану);
гідрометалургійний (електролізом із розчинів Cu, Zn, Ni, Co, Au, Ag);
порошкова металургія;
космічна металургія (ведеться у
вакумному середовищі, при
відсутності сили тяжіння).
Способи виробництва металів і сплавів:
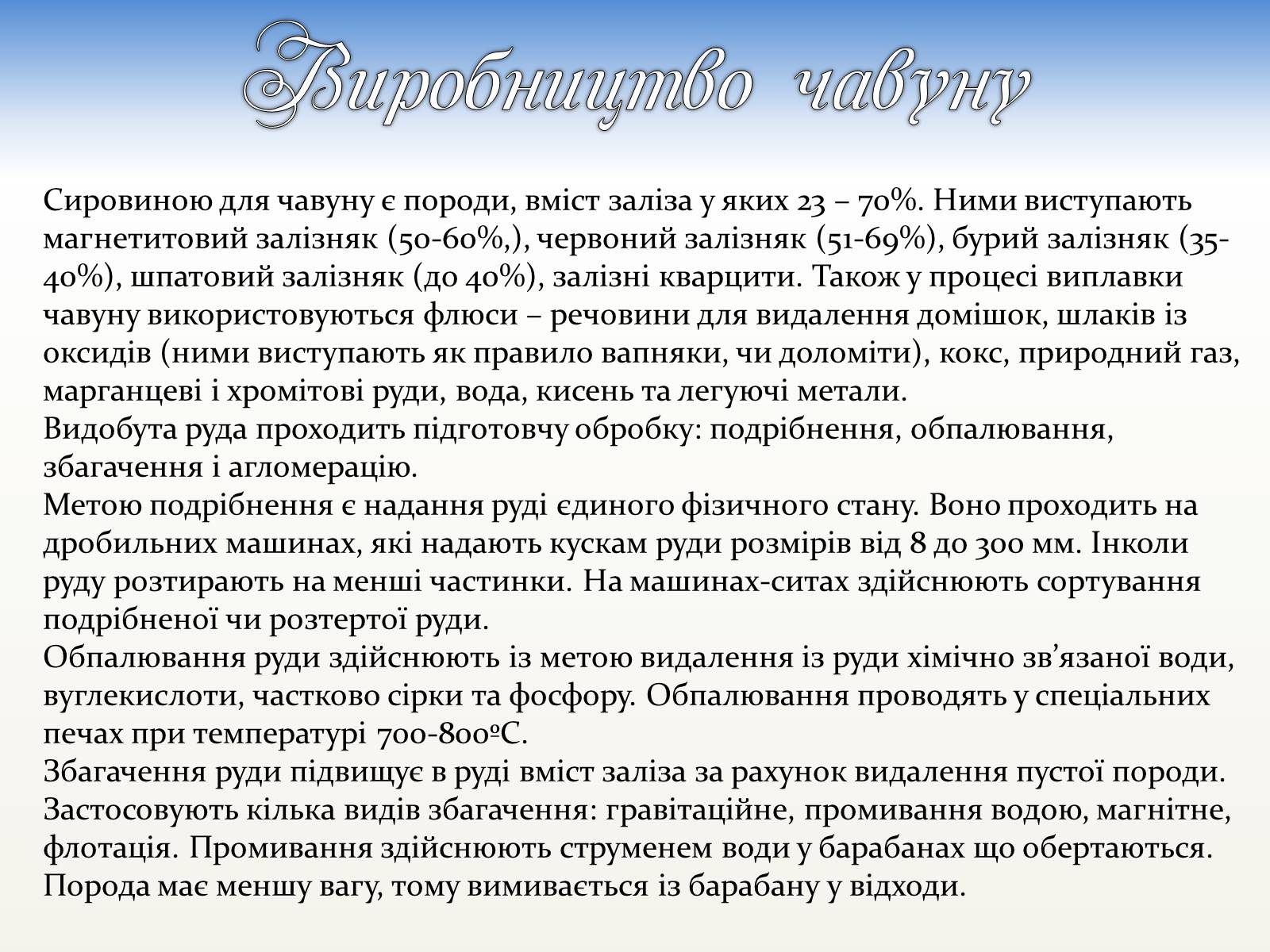
Сировиною для чавуну є породи, вміст заліза у яких 23 – 70%. Ними виступають магнетитовий залізняк (50-60%,), червоний залізняк (51-69%), бурий залізняк (35-40%), шпатовий залізняк (до 40%), залізні кварцити. Також у процесі виплавки чавуну використовуються флюси – речовини для видалення домішок, шлаків із оксидів (ними виступають як правило вапняки, чи доломіти), кокс, природний газ, марганцеві і хромітові руди, вода, кисень та легуючі метали.
Видобута руда проходить підготовчу обробку: подрібнення, обпалювання, збагачення і агломерацію.
Метою подрібнення є надання руді єдиного фізичного стану. Воно проходить на дробильних машинах, які надають кускам руди розмірів від 8 до 300 мм. Інколи руду розтирають на менші частинки. На машинах-ситах здійснюють сортування подрібненої чи розтертої руди.
Обпалювання руди здійснюють із метою видалення із руди хімічно зв'язаної води, вуглекислоти, частково сірки та фосфору. Обпалювання проводять у спеціальних печах при температурі 700-800ºC.
Збагачення руди підвищує в руді вміст заліза за рахунок видалення пустої породи. Застосовують кілька видів збагачення: гравітаційне, промивання водою, магнітне, флотація. Промивання здійснюють струменем води у барабанах що обертаються. Порода має меншу вагу, тому вимивається із барабану у відходи.
Виробництво чавуну
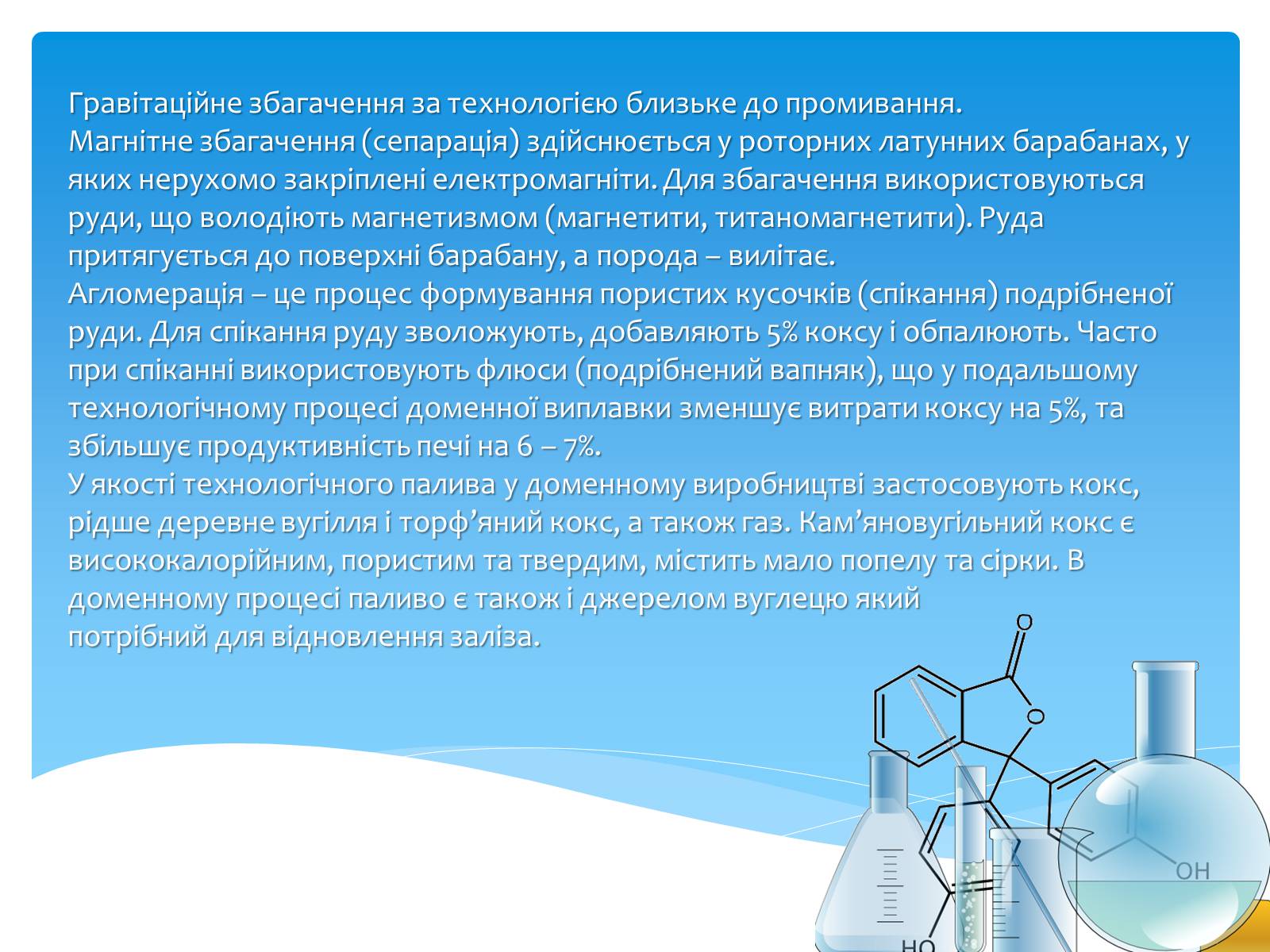
Гравітаційне збагачення за технологією близьке до промивання.
Магнітне збагачення (сепарація) здійснюється у роторних латунних барабанах, у яких нерухомо закріплені електромагніти. Для збагачення використовуються руди, що володіють магнетизмом (магнетити, титаномагнетити). Руда притягується до поверхні барабану, а порода – вилітає.
Агломерація – це процес формування пористих кусочків (спікання) подрібненої руди. Для спікання руду зволожують, добавляють 5% коксу і обпалюють. Часто при спіканні використовують флюси (подрібнений вапняк), що у подальшому технологічному процесі доменної виплавки зменшує витрати коксу на 5%, та збільшує продуктивність печі на 6 – 7%.
У якості технологічного палива у доменному виробництві застосовують кокс, рідше деревне вугілля і торф'яний кокс, а також газ. Кам'яновугільний кокс є висококалорійним, пористим та твердим, містить мало попелу та сірки. В доменному процесі паливо є також і джерелом вуглецю який
потрібний для відновлення заліза.
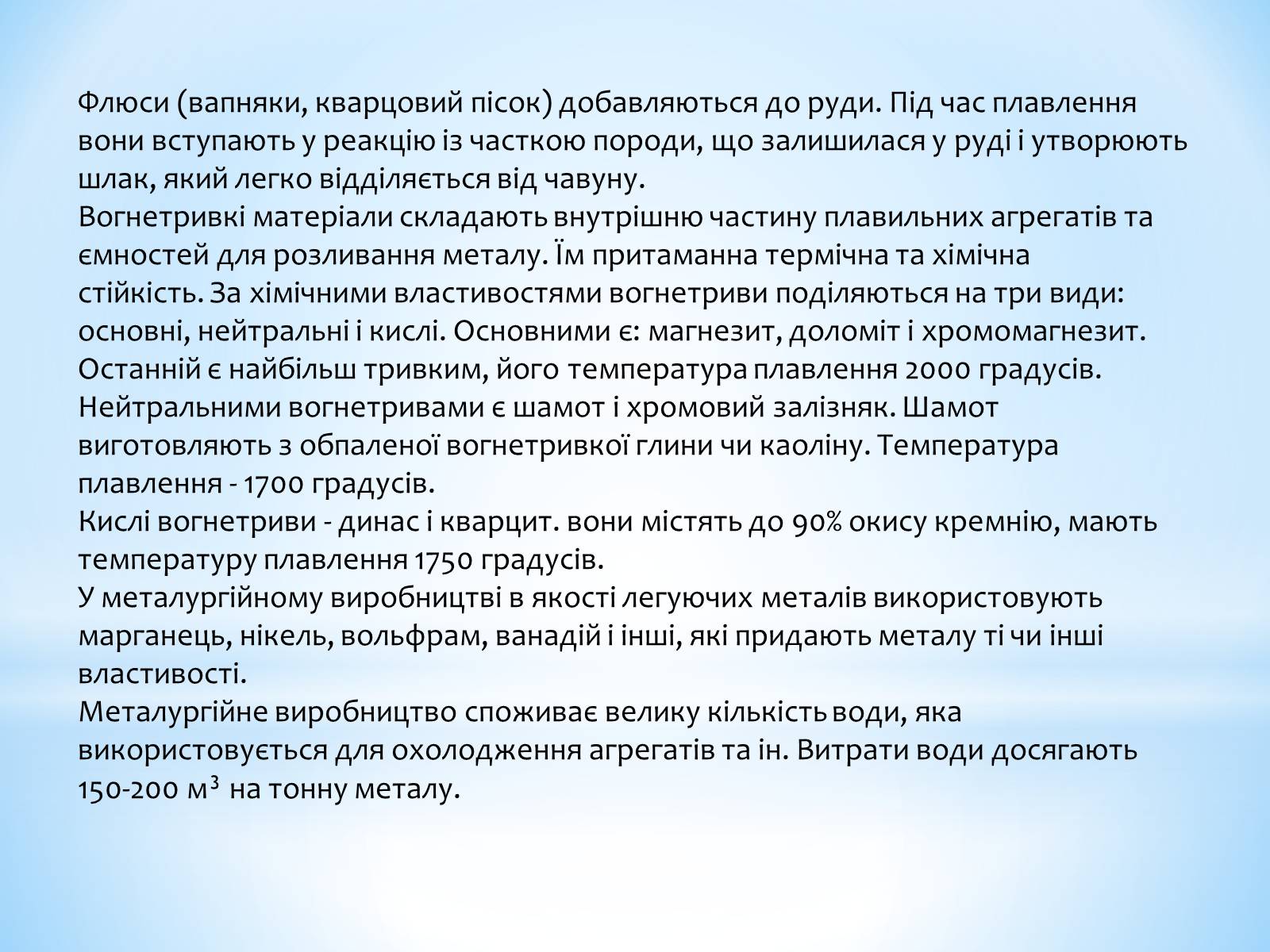
Флюси (вапняки, кварцовий пісок) добавляються до руди. Під час плавлення вони вступають у реакцію із часткою породи, що залишилася у руді і утворюють шлак, який легко відділяється від чавуну.
Вогнетривкі матеріали складають внутрішню частину плавильних агрегатів та ємностей для розливання металу. Їм притаманна термічна та хімічна стійкість. За хімічними властивостями вогнетриви поділяються на три види: основні, нейтральні і кислі. Основними є: магнезит, доломіт і хромомагнезит. Останній є найбільш тривким, його температура плавлення 2000 градусів.
Нейтральними вогнетривами є шамот і хромовий залізняк. Шамот виготовляють з обпаленої вогнетривкої глини чи каоліну. Температура плавлення - 1700 градусів.
Кислі вогнетриви - динас і кварцит. вони містять до 90% окису кремнію, мають температуру плавлення 1750 градусів.
У металургійному виробництві в якості легуючих металів використовують марганець, нікель, вольфрам, ванадій і інші, які придають металу ті чи інші властивості.
Металургійне виробництво споживає велику кількість води, яка використовується для охолодження агрегатів та ін. Витрати води досягають 150-200 м³ на тонну металу.

Чавун варять у печах-домнах. Доменний цех металургійного заводу має від 1 до 10 доменних печей, рудний двір, підйомні і вантажні агрегати, повітронагрівачі і газоочисники.
Доменна піч – промислова піч для виплавки доменного чавуну. Це вертикальна споруда (30 –
40 м висоти) внутрішня частина якої викладена вогнетривким матеріалом – шамотом, а зовнішня представлена зварним стальним кожухом. Об'єм печі – від 3 до 5 тис. м³. Основні частини такі: колошник, шахта, розпар, заплечики, горно, лещадь(черінь).
Колошник - верхня частина печі. Тут завантажують шихту. Є газовідводи для доменного і колошникового газу. Температура шихти в колошнику досягає 150 - 300ºC. Шахта – найбільша частина печі, що знаходиться під колошником. Тут температура досягає до 1200ºC.
Доменне виробництво
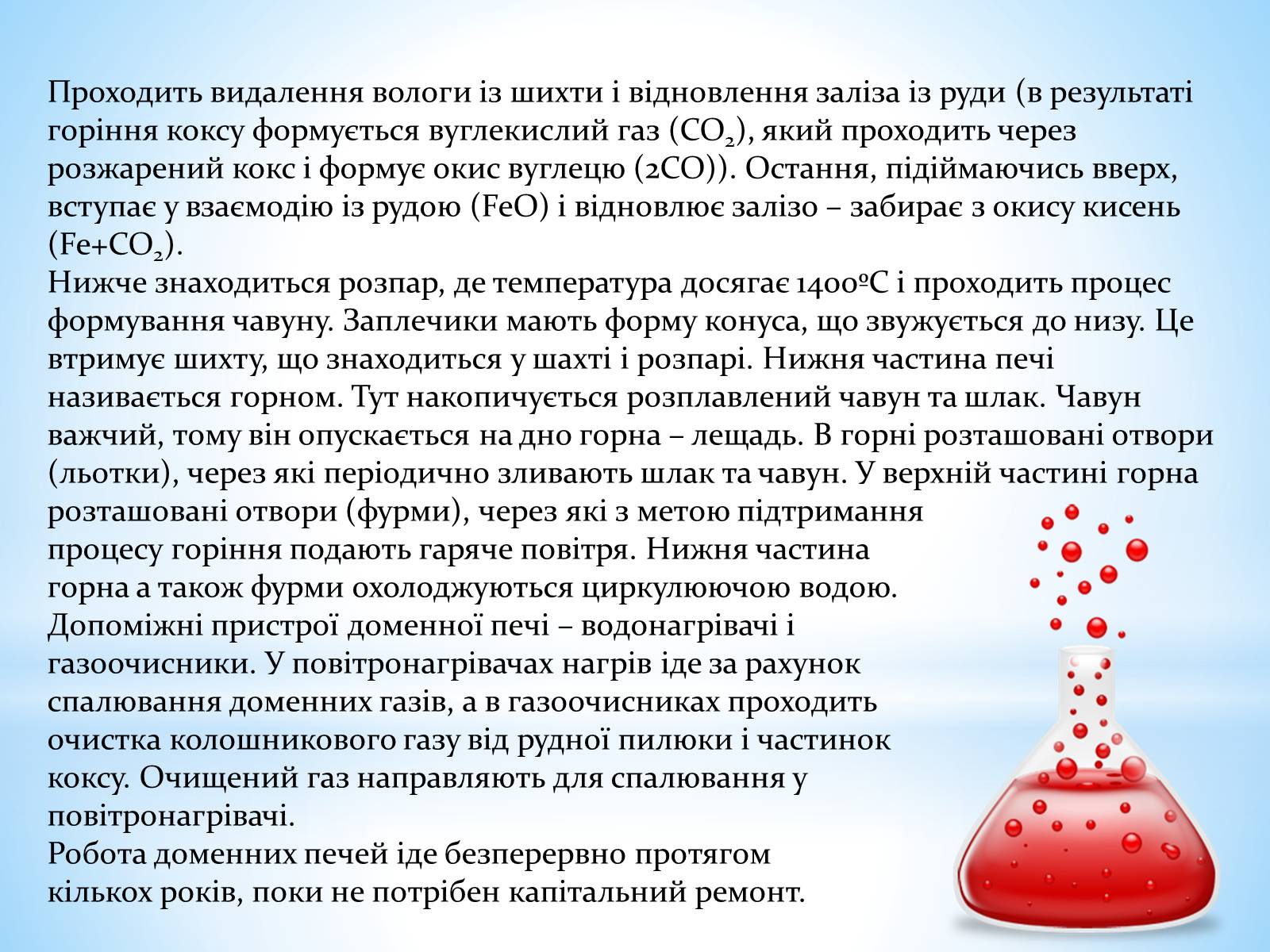
Проходить видалення вологи із шихти і відновлення заліза із руди (в результаті горіння коксу формується вуглекислий газ (СО2), який проходить через розжарений кокс і формує окис вуглецю (2СО)). Остання, підіймаючись вверх, вступає у взаємодію із рудою (FeО) і відновлює залізо – забирає з окису кисень (Fe+СО2).
Нижче знаходиться розпар, де температура досягає 1400ºC і проходить процес формування чавуну. Заплечики мають форму конуса, що звужується до низу. Це втримує шихту, що знаходиться у шахті і розпарі. Нижня частина печі називається горном. Тут накопичується розплавлений чавун та шлак. Чавун важчий, тому він опускається на дно горна – лещадь. В горні розташовані отвори (льотки), через які періодично зливають шлак та чавун. У верхній частині горна розташовані отвори (фурми), через які з метою підтримання процесу горіння подають гаряче повітря. Нижня частина горна а також фурми охолоджуються циркулюючою водою.
Допоміжні пристрої доменної печі – водонагрівачі і газоочисники. У повітронагрівачах нагрів іде за рахунок спалювання доменних газів, а в газоочисниках проходить очистка колошникового газу від рудної пилюки і частинок коксу. Очищений газ направляють для спалювання у повітронагрівачі.
Робота доменних печей іде безперервно протягом кількох років, поки не потрібен капітальний ремонт.
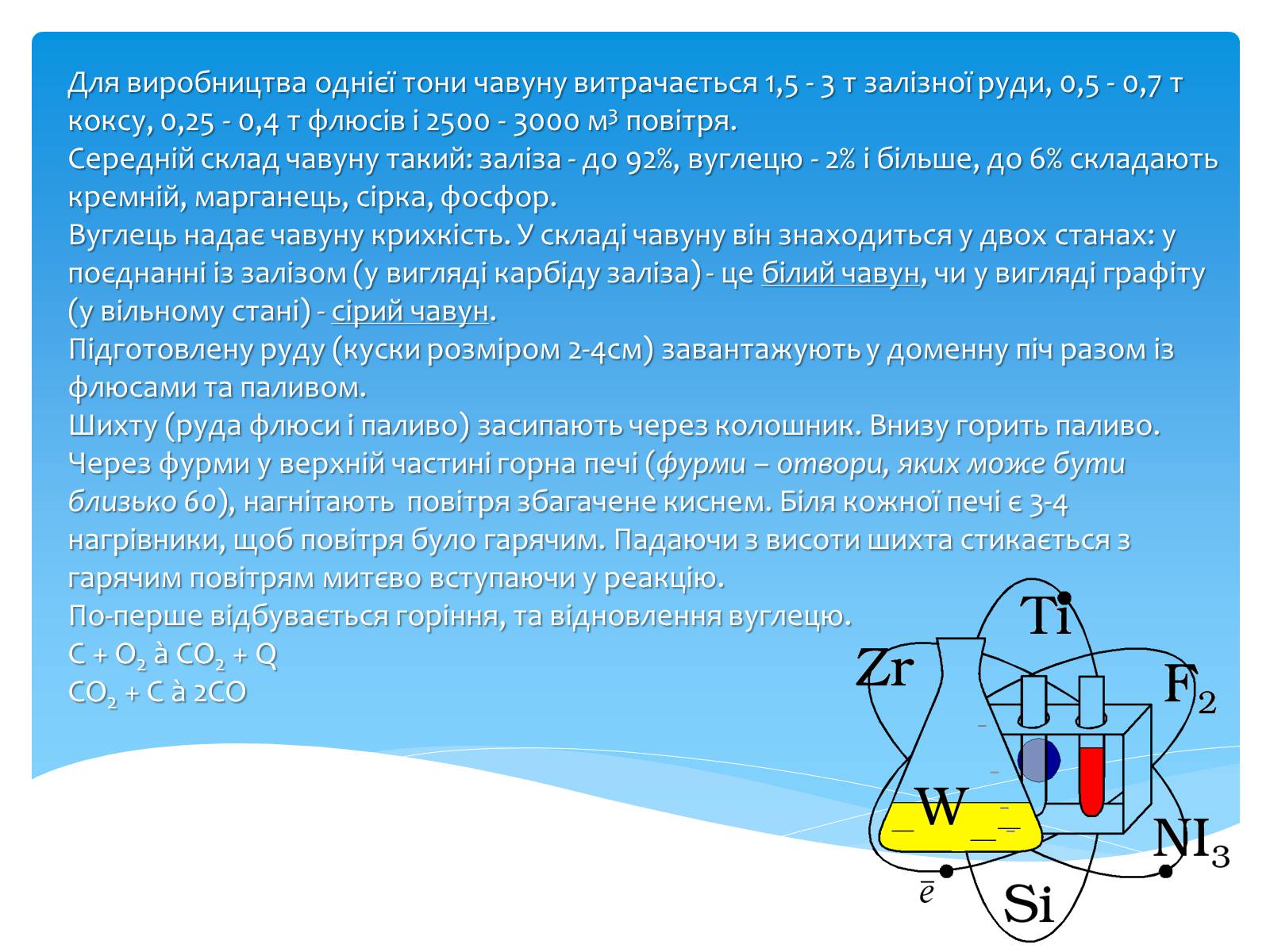
Для виробництва однієї тони чавуну витрачається 1,5 - 3 т залізної руди, 0,5 - 0,7 т коксу, 0,25 - 0,4 т флюсів і 2500 - 3000 м3 повітря.
Середній склад чавуну такий: заліза - до 92%, вуглецю - 2% і більше, до 6% складають кремній, марганець, сірка, фосфор.
Вуглець надає чавуну крихкість. У складі чавуну він знаходиться у двох станах: у поєднанні із залізом (у вигляді карбіду заліза) - це білий чавун, чи у вигляді графіту (у вільному стані) - сірий чавун.
Підготовлену руду (куски розміром 2-4см) завантажують у доменну піч разом із флюсами та паливом.
Шихту (руда флюси і паливо) засипають через колошник. Внизу горить паливо. Через фурми у верхній частині горна печі (фурми – отвори, яких може бути близько 60), нагнітають повітря збагачене киснем. Біля кожної печі є 3-4 нагрівники, щоб повітря було гарячим. Падаючи з висоти шихта стикається з гарячим повітрям митєво вступаючи у реакцію. По-перше відбувається горіння, та відновлення вуглецю.
С + О2 à СО2 + Q
CO2 + C à 2CO
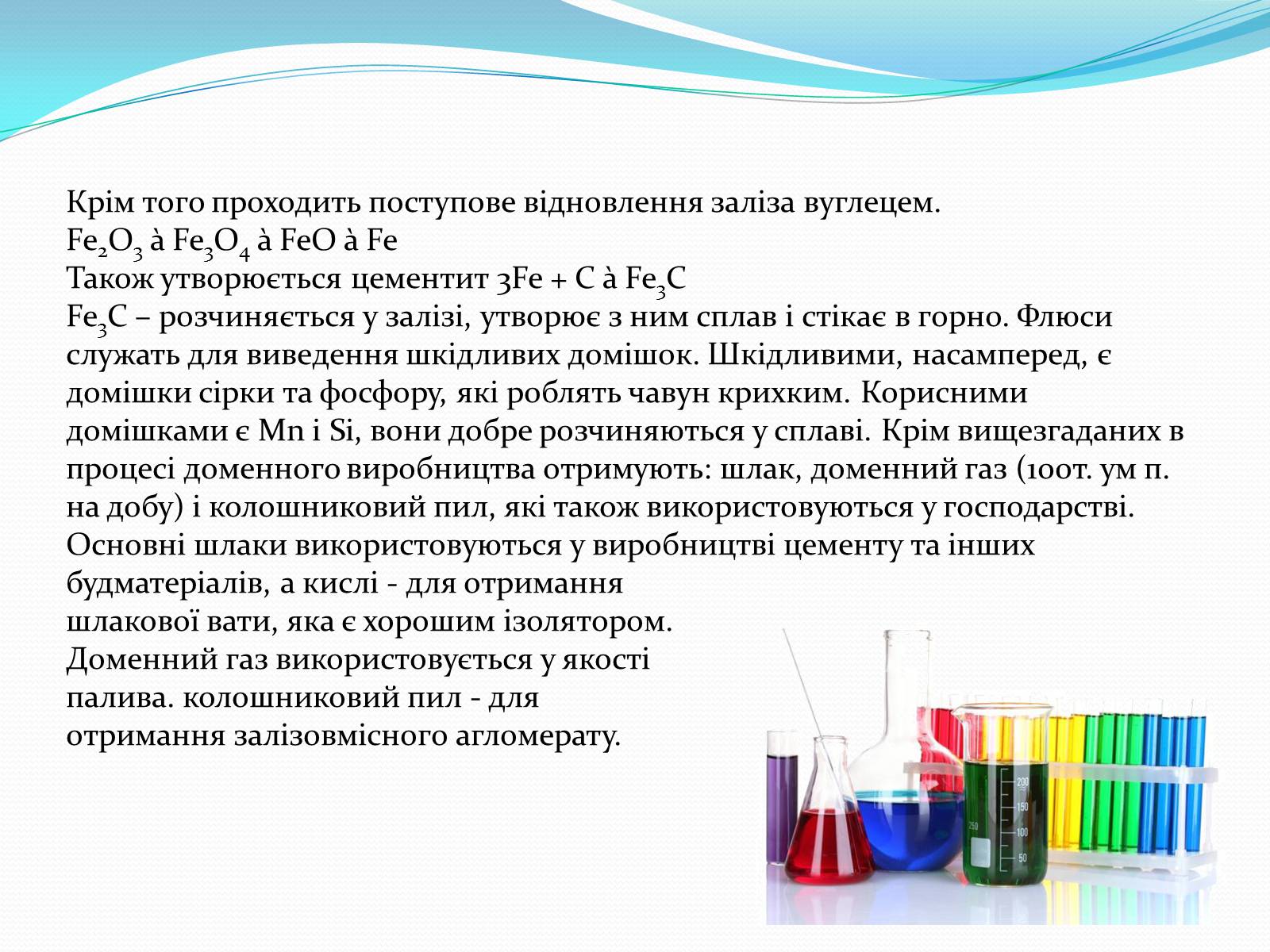
Крім того проходить поступове відновлення заліза вуглецем.
Fe2O3 à Fe3O4 à FeO à Fe
Також утворюється цементит 3Fe + C à Fe3C
Fe3C – розчиняється у залізі, утворює з ним сплав і стікає в горно. Флюси служать для виведення шкідливих домішок. Шкідливими, насамперед, є домішки сірки та фосфору, які роблять чавун крихким. Корисними домішками є Mn i Si, вони добре розчиняються у сплаві. Крім вищезгаданих в процесі доменного виробництва отримують: шлак, доменний газ (100т. ум п. на добу) і колошниковий пил, які також використовуються у господарстві. Основні шлаки використовуються у виробництві цементу та інших будматеріалів, а кислі - для отримання
шлакової вати, яка є хорошим ізолятором.
Доменний газ використовується у якості
палива. колошниковий пил - для
отримання залізовмісного агломерату.
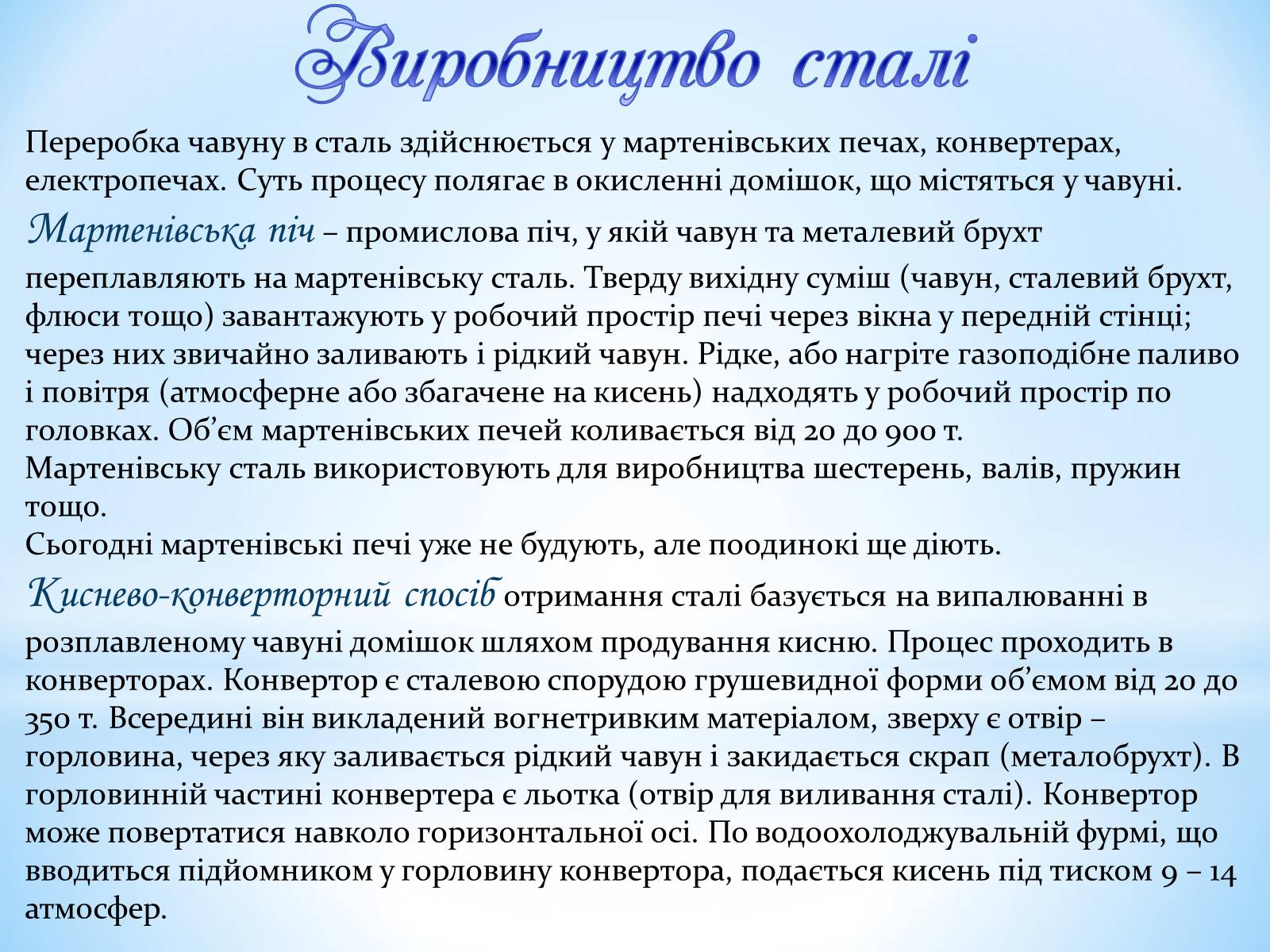
Переробка чавуну в сталь здійснюється у мартенівських печах, конвертерах, електропечах. Суть процесу полягає в окисленні домішок, що містяться у чавуні.
Мартенівська піч – промислова піч, у якій чавун та металевий брухт переплавляють на мартенівську сталь. Тверду вихідну суміш (чавун, сталевий брухт, флюси тощо) завантажують у робочий простір печі через вікна у передній стінці; через них звичайно заливають і рідкий чавун. Рідке, або нагріте газоподібне паливо і повітря (атмосферне або збагачене на кисень) надходять у робочий простір по головках. Об'єм мартенівських печей коливається від 20 до 900 т.
Мартенівську сталь використовують для виробництва шестерень, валів, пружин тощо.
Сьогодні мартенівські печі уже не будують, але поодинокі ще діють.
Киснево-конверторний спосіб отримання сталі базується на випалюванні в розплавленому чавуні домішок шляхом продування кисню. Процес проходить в конверторах. Конвертор є сталевою спорудою грушевидної форми об'ємом від 20 до 350 т. Всередині він викладений вогнетривким матеріалом, зверху є отвір – горловина, через яку заливається рідкий чавун і закидається скрап (металобрухт). В горловинній частині конвертера є льотка (отвір для виливання сталі). Конвертор може повертатися навколо горизонтальної осі. По водоохолоджувальній фурмі, що вводиться підйомником у горловину конвертора, подається кисень під тиском 9 – 14 атмосфер.
Виробництво сталі
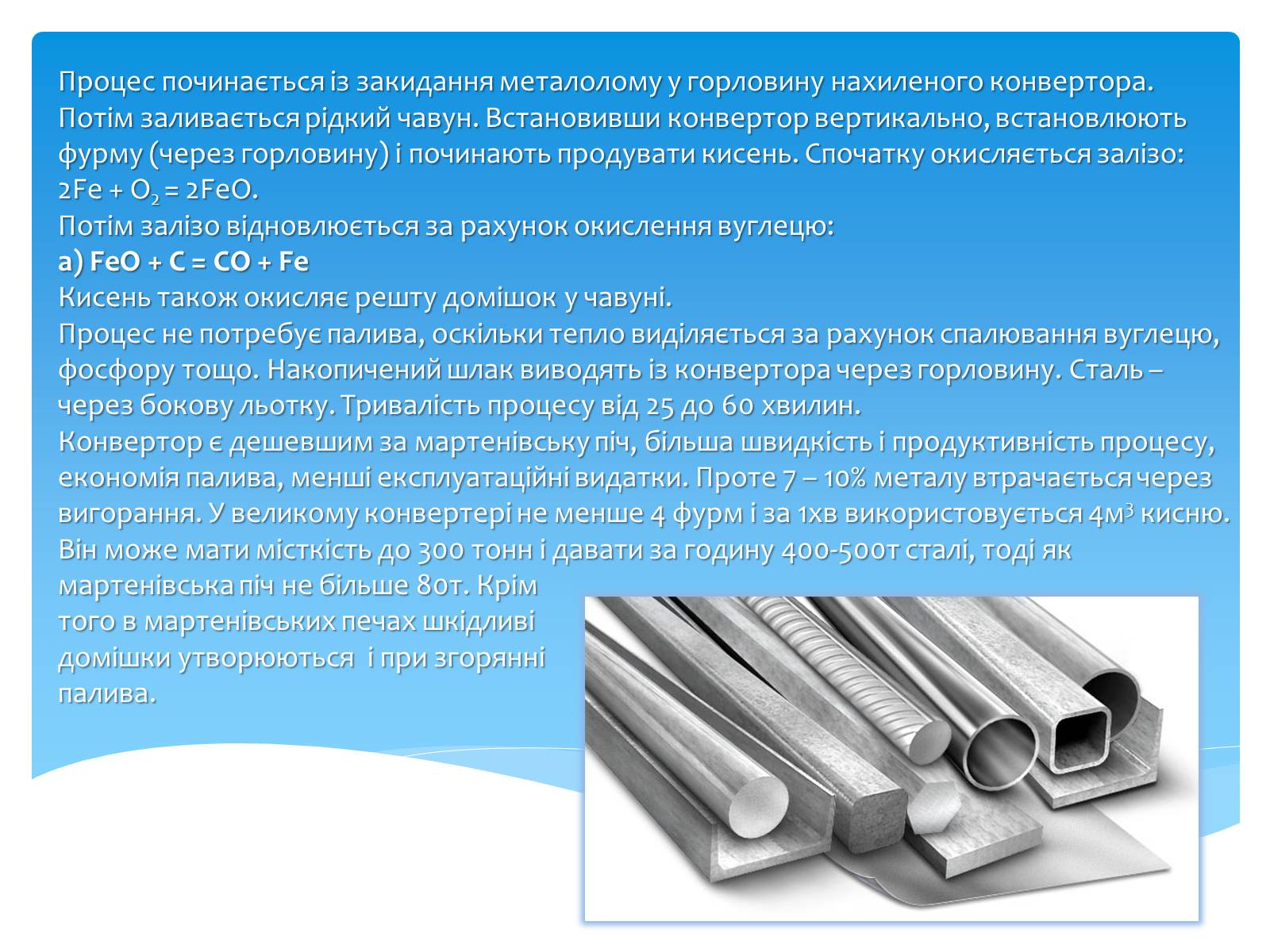
Процес починається із закидання металолому у горловину нахиленого конвертора. Потім заливається рідкий чавун. Встановивши конвертор вертикально, встановлюють фурму (через горловину) і починають продувати кисень. Спочатку окисляється залізо:
2Fe + O2 = 2FeO.
Потім залізо відновлюється за рахунок окислення вуглецю:
a) FeО + С = СО + Fe
Кисень також окисляє решту домішок у чавуні.
Процес не потребує палива, оскільки тепло виділяється за рахунок спалювання вуглецю, фосфору тощо. Накопичений шлак виводять із конвертора через горловину. Сталь – через бокову льотку. Тривалість процесу від 25 до 60 хвилин.
Конвертор є дешевшим за мартенівську піч, більша швидкість і продуктивність процесу, економія палива, менші експлуатаційні видатки. Проте 7 – 10% металу втрачається через вигорання. У великому конвертері не менше 4 фурм і за 1хв використовується 4м3 кисню. Він може мати місткість до 300 тонн і давати за годину 400-500т сталі, тоді як мартенівська піч не більше 80т. Крім
того в мартенівських печах шкідливі
домішки утворюються і при згорянні
палива.
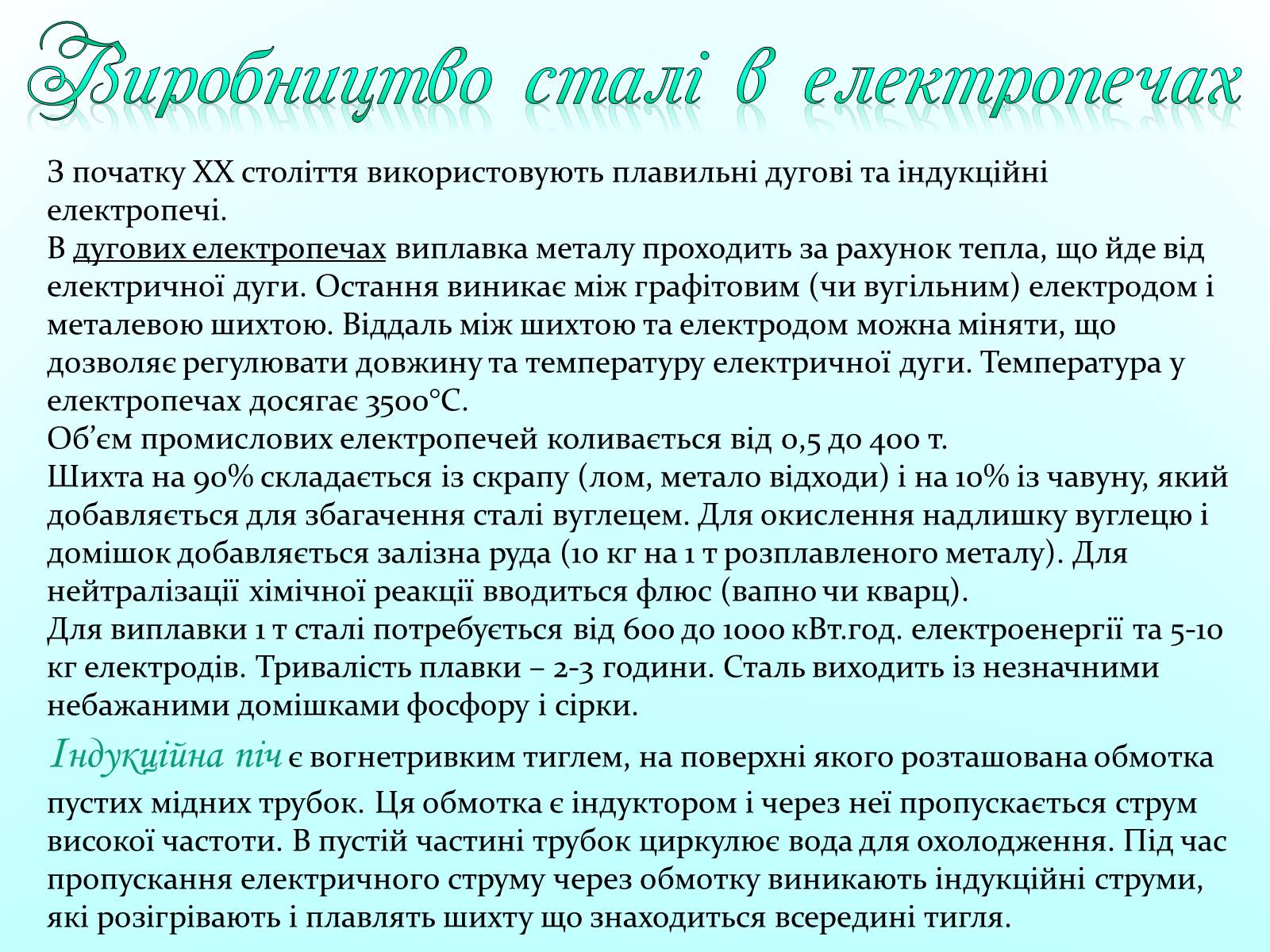
З початку ХХ століття використовують плавильні дугові та індукційні електропечі.
В дугових електропечах виплавка металу проходить за рахунок тепла, що йде від електричної дуги. Остання виникає між графітовим (чи вугільним) електродом і металевою шихтою. Віддаль між шихтою та електродом можна міняти, що дозволяє регулювати довжину та температуру електричної дуги. Температура у електропечах досягає 3500°C.
Об'єм промислових електропечей коливається від 0,5 до 400 т.
Шихта на 90% складається із скрапу (лом, метало відходи) і на 10% із чавуну, який добавляється для збагачення сталі вуглецем. Для окислення надлишку вуглецю і домішок добавляється залізна руда (10 кг на 1 т розплавленого металу). Для нейтралізації хімічної реакції вводиться флюс (вапно чи кварц).
Для виплавки 1 т сталі потребується від 600 до 1000 кВт.год. електроенергії та 5-10 кг електродів. Тривалість плавки – 2-3 години. Сталь виходить із незначними небажаними домішками фосфору і сірки.
Індукційна піч є вогнетривким тиглем, на поверхні якого розташована обмотка пустих мідних трубок. Ця обмотка є індуктором і через неї пропускається струм високої частоти. В пустій частині трубок циркулює вода для охолодження. Під час пропускання електричного струму через обмотку виникають індукційні струми, які розігрівають і плавлять шихту що знаходиться всередині тигля.
Виробництво сталі в електропечах
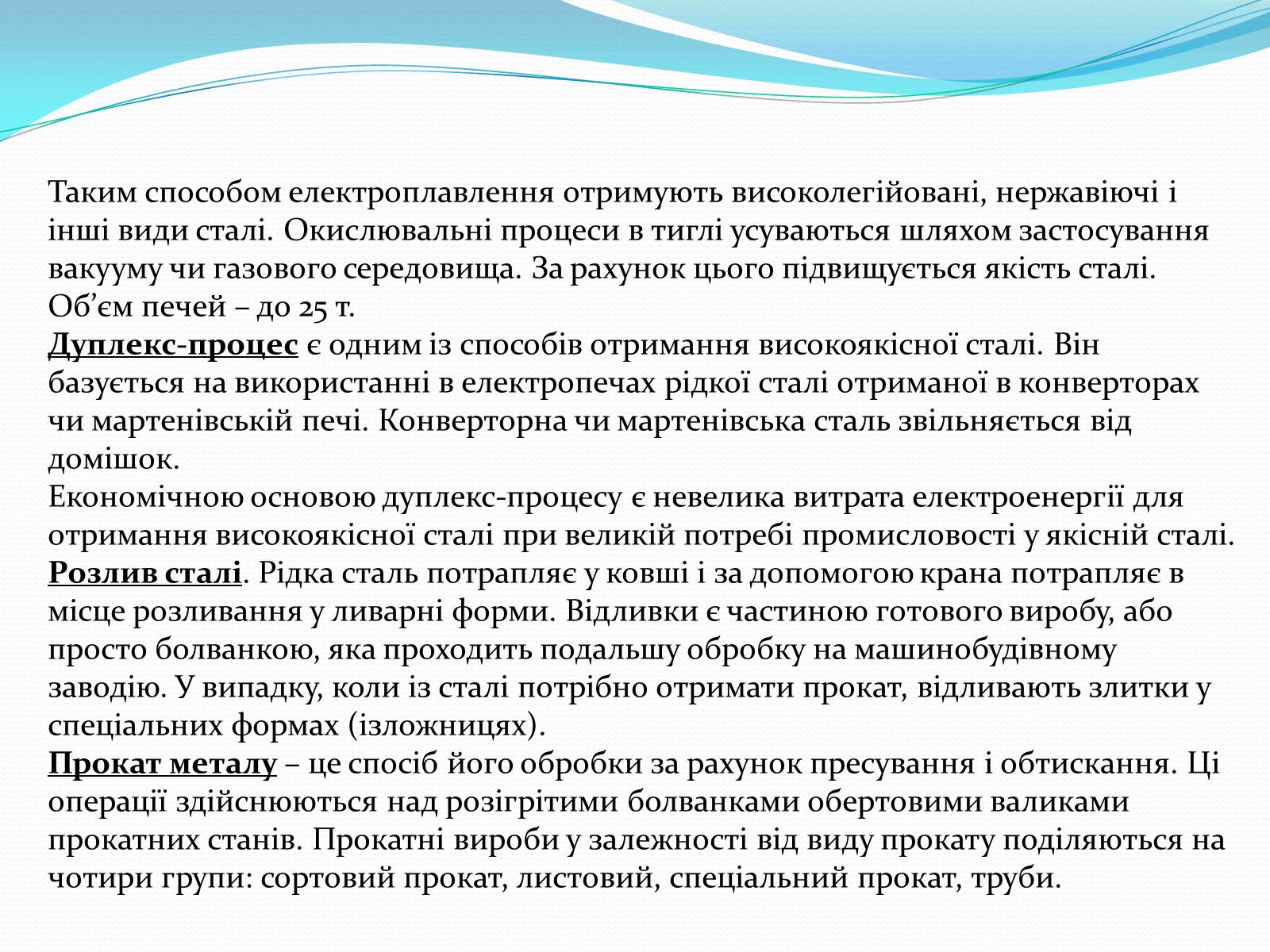
Таким способом електроплавлення отримують високолегійовані, нержавіючі і інші види сталі. Окислювальні процеси в тиглі усуваються шляхом застосування вакууму чи газового середовища. За рахунок цього підвищується якість сталі. Об'єм печей – до 25 т.
Дуплекс-процес є одним із способів отримання високоякісної сталі. Він базується на використанні в електропечах рідкої сталі отриманої в конверторах чи мартенівській печі. Конверторна чи мартенівська сталь звільняється від домішок.
Економічною основою дуплекс-процесу є невелика витрата електроенергії для отримання високоякісної сталі при великій потребі промисловості у якісній сталі.
Розлив сталі. Рідка сталь потрапляє у ковші і за допомогою крана потрапляє в місце розливання у ливарні форми. Відливки є частиною готового виробу, або просто болванкою, яка проходить подальшу обробку на машинобудівному заводію. У випадку, коли із сталі потрібно отримати прокат, відливають злитки у спеціальних формах (ізложницях).
Прокат металу – це спосіб його обробки за рахунок пресування і обтискання. Ці операції здійснюються над розігрітими болванками обертовими валиками прокатних станів. Прокатні вироби у залежності від виду прокату поділяються на чотири групи: сортовий прокат, листовий, спеціальний прокат, труби.
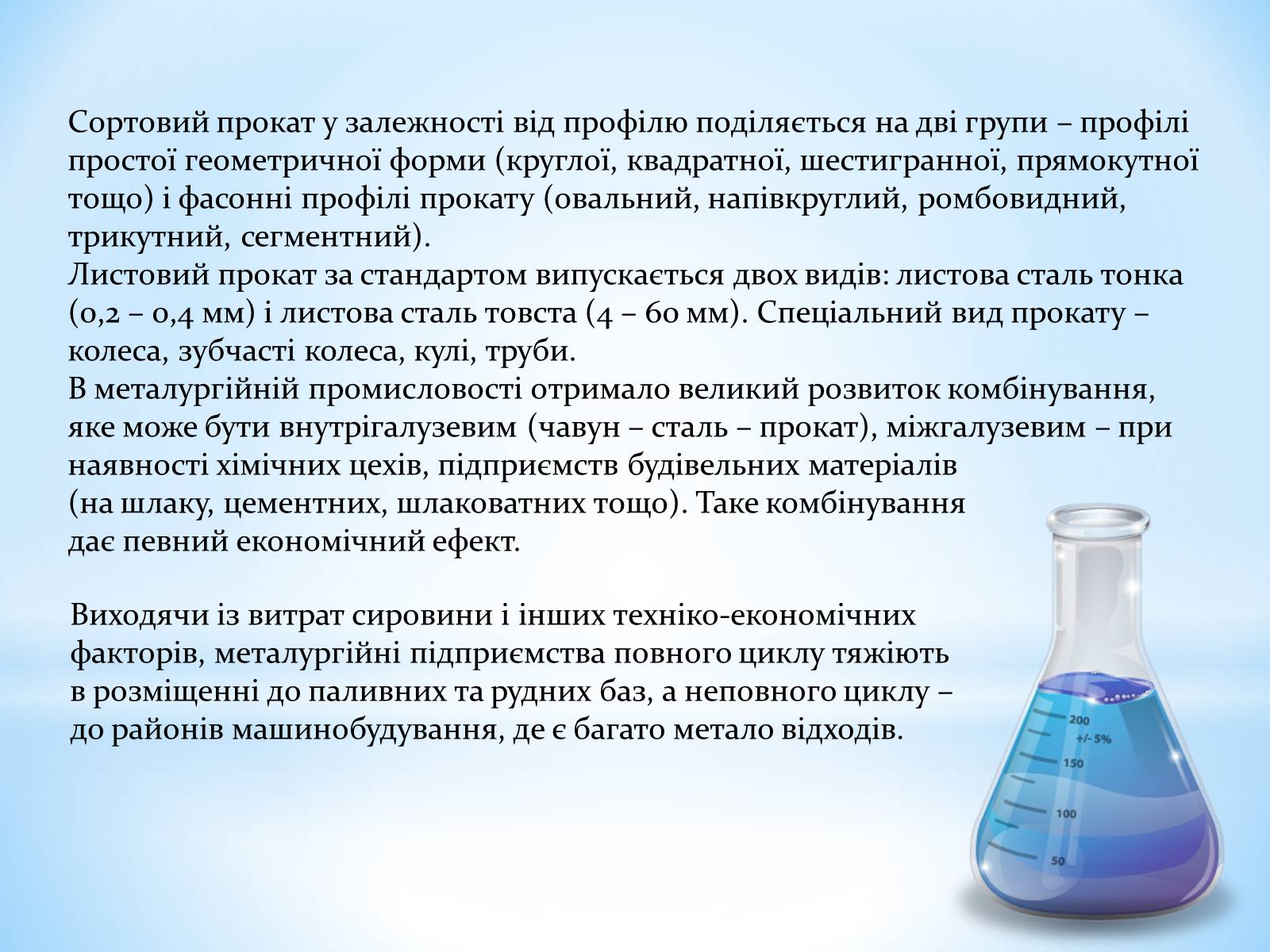
Сортовий прокат у залежності від профілю поділяється на дві групи – профілі простої геометричної форми (круглої, квадратної, шестигранної, прямокутної тощо) і фасонні профілі прокату (овальний, напівкруглий, ромбовидний, трикутний, сегментний).
Листовий прокат за стандартом випускається двох видів: листова сталь тонка (0,2 – 0,4 мм) і листова сталь товста (4 – 60 мм). Спеціальний вид прокату – колеса, зубчасті колеса, кулі, труби.
В металургійній промисловості отримало великий розвиток комбінування, яке може бути внутрігалузевим (чавун – сталь – прокат), міжгалузевим – при наявності хімічних цехів, підприємств будівельних матеріалів
(на шлаку, цементних, шлаковатних тощо). Таке комбінування
дає певний економічний ефект.
Виходячи із витрат сировини і інших техніко-економічних факторів, металургійні підприємства повного циклу тяжіють в розміщенні до паливних та рудних баз, а неповного циклу – до районів машинобудування, де є багато метало відходів.
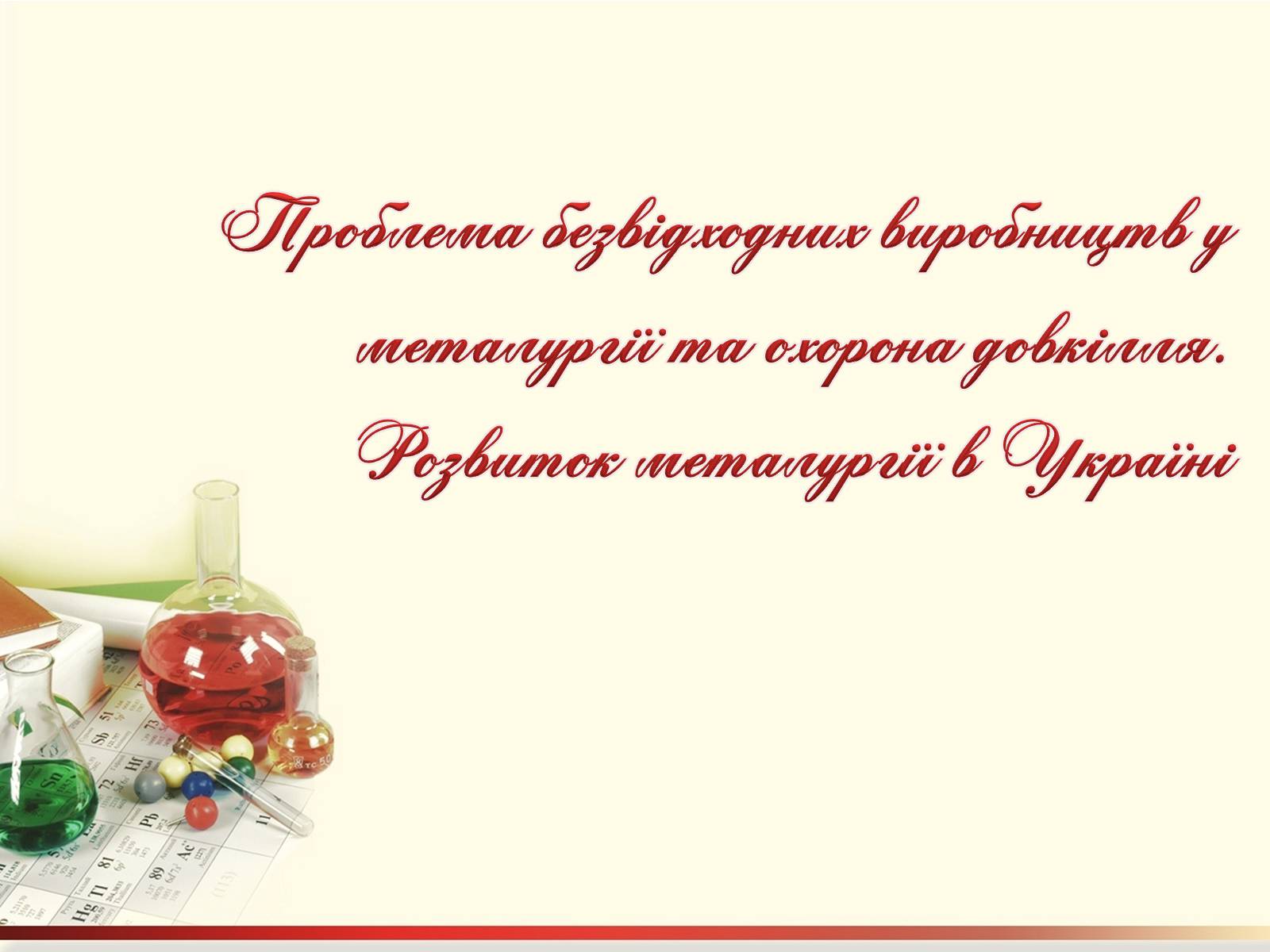
Проблема безвідходних виробництв у металургії та охорона довкілля. Розвиток металургії вУкраїні
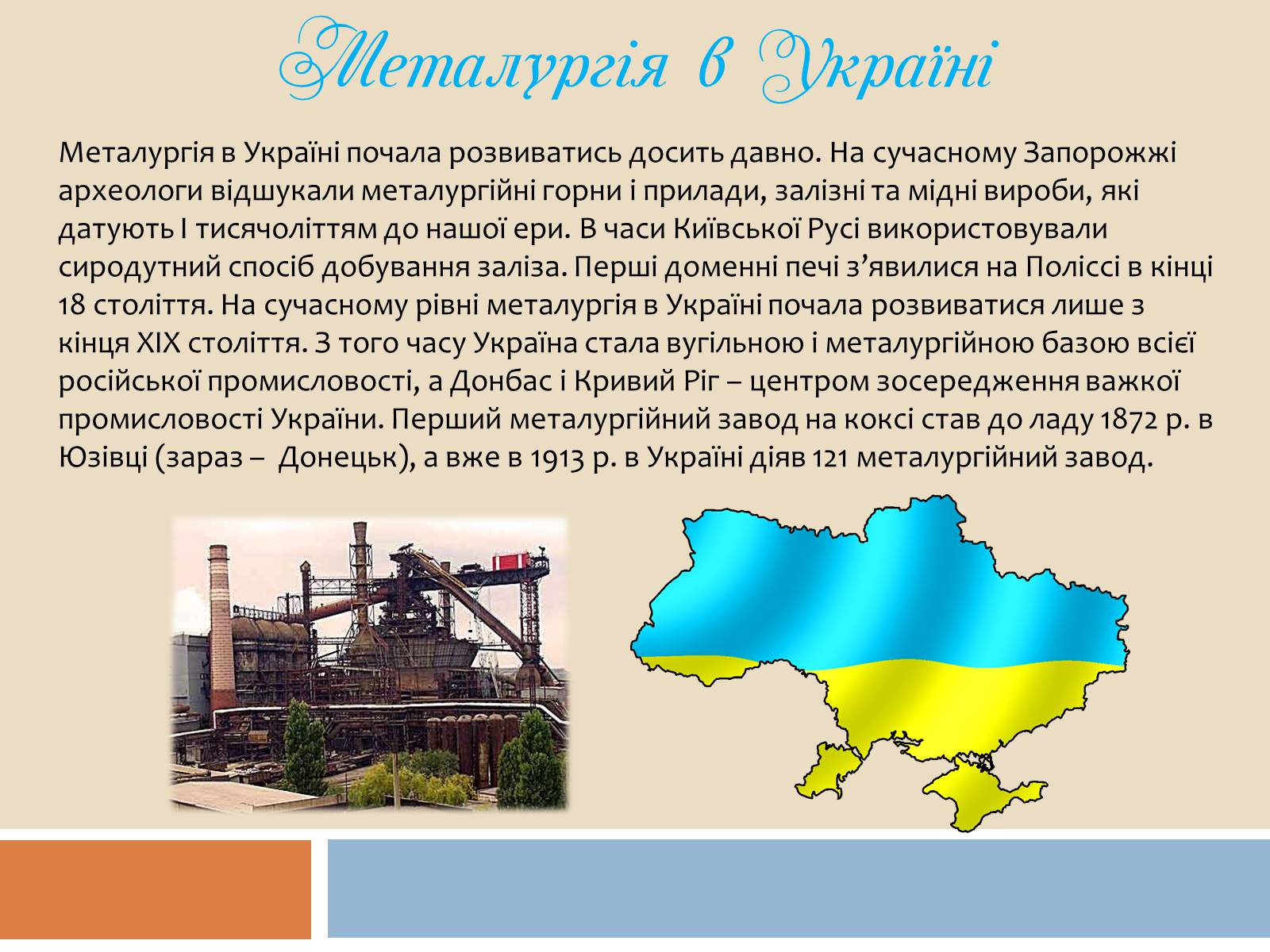
Металургія в Україні почала розвиватись досить давно. На сучасному Запорожжі археологи відшукали металургійні горни і прилади, залізні та мідні вироби, які датують І тисячоліттям до нашої ери. В часи Київської Русі використовували сиродутний спосіб добування заліза. Перші доменні печі з'явилися на Поліссі в кінці 18 століття. На сучасному рівні металургія в Україні почала розвиватися лише з кінця XIX століття. З того часу Україна стала вугільною і металургійною базою всієї російської промисловості, а Донбас і Кривий Ріг – центром зосередження важкої промисловості України. Перший металургійний завод на коксі став до ладу 1872 р. в Юзівці (зараз – Донецьк), а вже в 1913 р. в Україні діяв 121 металургійний завод.
Металургія в Україні
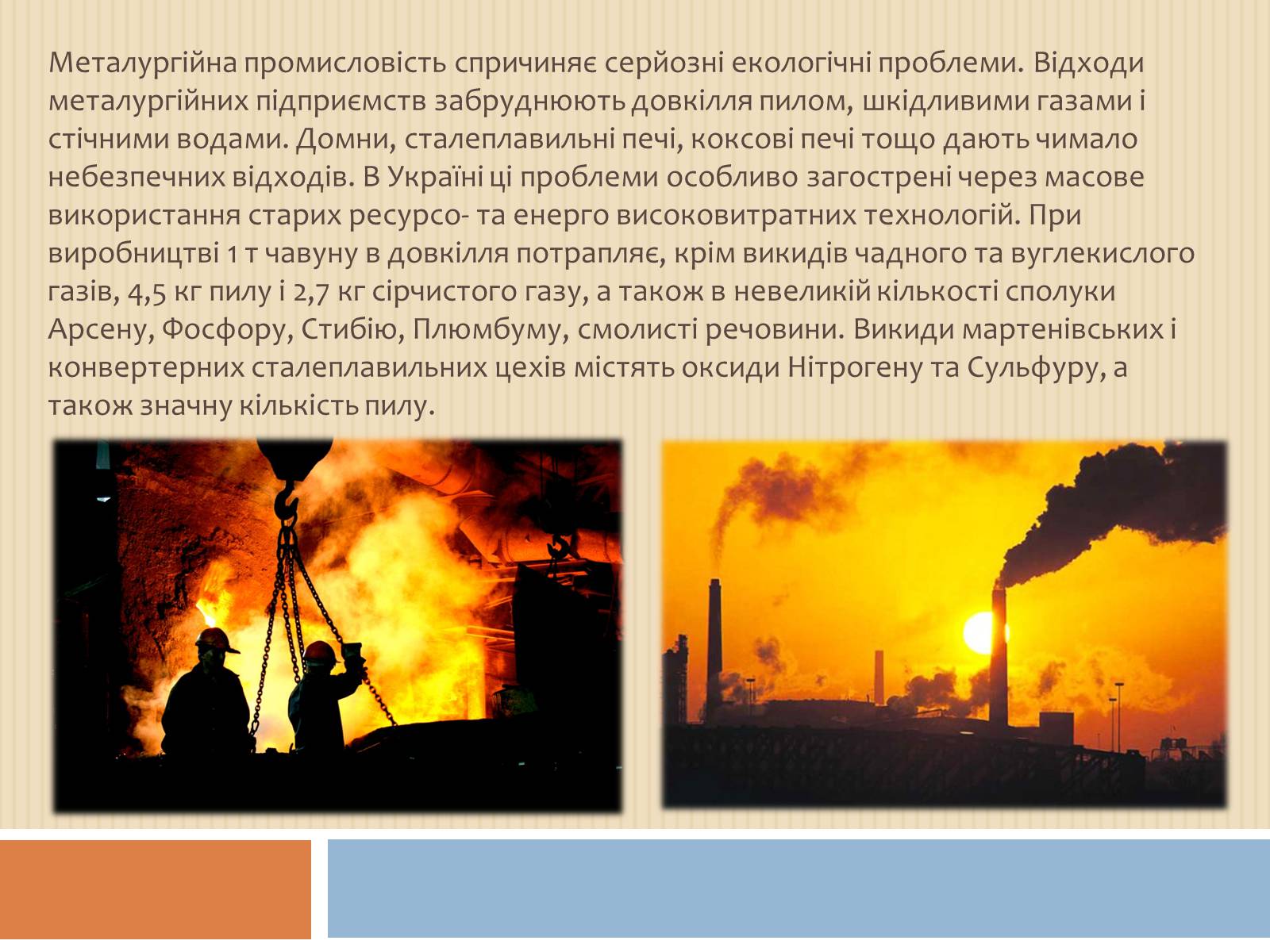
Металургійна промисловість спричиняє серйозні екологічні проблеми. Відходи металургійних підприємств забруднюють довкілля пилом, шкідливими газами і стічними водами. Домни, сталеплавильні печі, коксові печі тощо дають чимало небезпечних відходів. В Україні ці проблеми особливо загострені через масове використання старих ресурсо- та енерго високовитратних технологій. При виробництві 1 т чавуну в довкілля потрапляє, крім викидів чадного та вуглекислого газів, 4,5 кг пилу і 2,7 кг сірчистого газу, а також в невеликій кількості сполуки Арсену, Фосфору, Стибію, Плюмбуму, смолисті речовини. Викиди мартенівських і конвертерних сталеплавильних цехів містять оксиди Нітрогену та Сульфуру, а також значну кількість пилу.
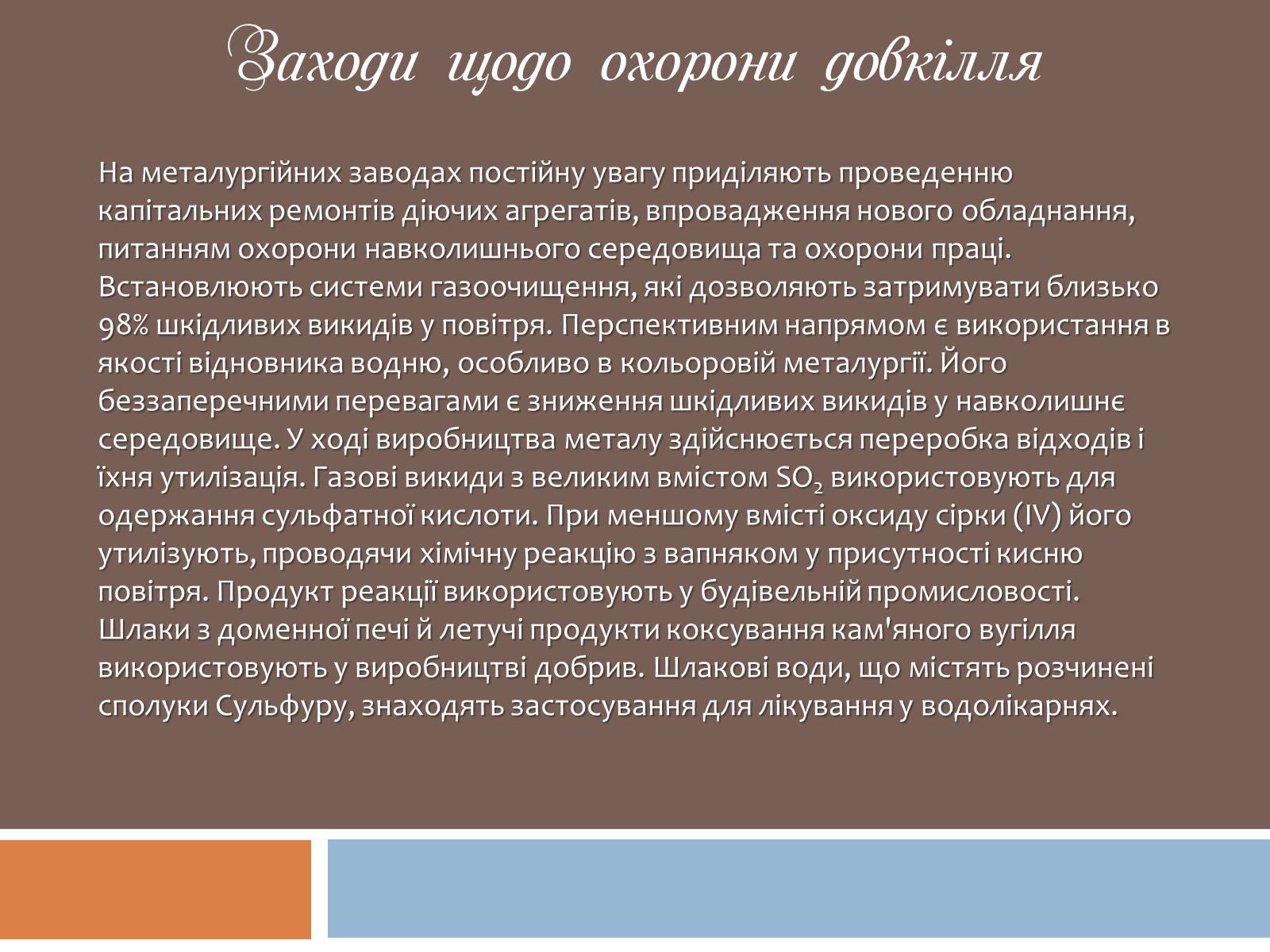
На металургійних заводах постійну увагу приділяють проведенню капітальних ремонтів діючих агрегатів, впровадження нового обладнання, питанням охорони навколишнього середовища та охорони праці. Встановлюють системи газоочищення, які дозволяють затримувати близько 98% шкідливих викидів у повітря. Перспективним напрямом є використання в якості відновника водню, особливо в кольоровій металургії. Його беззаперечними перевагами є зниження шкідливих викидів у навколишнє середовище. У ході виробництва металу здійснюється переробка відходів і їхня утилізація. Газові викиди з великим вмістом SO2 використовують для одержання сульфатної кислоти. При меншому вмісті оксиду сірки (IV) його утилізують, проводячи хімічну реакцію з вапняком у присутності кисню повітря. Продукт реакції використовують у будівельній промисловості. Шлаки з доменної печі й летучі продукти коксування кам'яного вугілля використовують у виробництві добрив. Шлакові води, що містять розчинені сполуки Сульфуру, знаходять застосування для лікування у водолікарнях.
Заходи щодо охорони довкілля
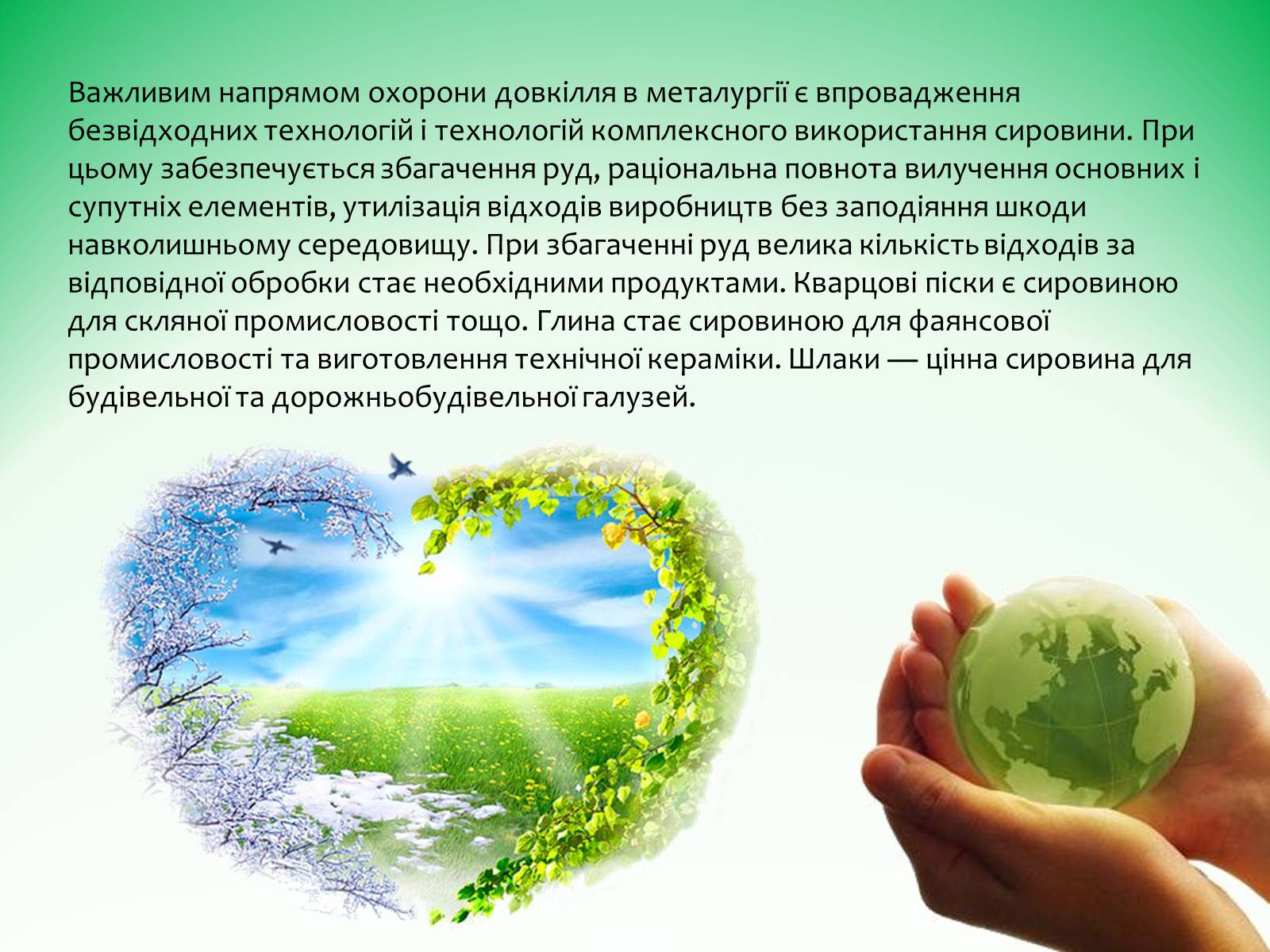
Важливим напрямом охорони довкілля в металургії є впровадження безвідходних технологій і технологій комплексного використання сировини. При цьому забезпечується збагачення руд, раціональна повнота вилучення основних і супутніх елементів, утилізація відходів виробництв без заподіяння шкоди навколишньому середовищу. При збагаченні руд велика кількість відходів за відповідної обробки стає необхідними продуктами. Кварцові піски є сировиною для скляної промисловості тощо. Глина стає сировиною для фаянсової промисловості та виготовлення технічної кераміки. Шлаки ― цінна сировина для будівельної та дорожньобудівельної галузей.